This information is preliminary and subject to change.
On February 6, 2024, about 15:55 eastern standard time, United Airlines (UAL) flight 1539, a Boeing 737-8, N47280, experienced “stuck” rudder pedals during the landing rollout at Newark Liberty International Airport (EWR), Newark, New Jersey. The airplane taxied to the gate without further incident and all occupants (2 flight crewmembers, 4 cabin crewmembers, and 155 passengers) deplaned at the gate without any injuries. The flight was operating under the provisions of Title 14 Code of Federal Regulations Part 121 as a scheduled international passenger flight from Lynden Pindling International Airport (NAS), Nassau, Bahamas to EWR.
In a post-incident statement, the captain reported that during the landing rollout, the rudder pedals did not move in response to the “normal” application of foot pressure while attempting to maintain the runway centerline. The pedals remained “stuck” in their neutral position. The captain used the nosewheel steering tiller to keep the airplane near the runway centerline while slowing to a safe taxi speed before exiting the runway onto a high-speed turn-off. While on the high-speed turnoff, the captain asked the first officer to check his rudder pedals and he reported the same problem. The captain reported, that shortly thereafter, the rudder pedals began to operate normally. After parking the aircraft, the flight crew notified UAL maintenance of the flight control malfunction. The airplane was removed from service for maintenance and troubleshooting.
A review of preliminary flight data recorder (FDR) data corroborated the pilot’s statements regarding the malfunction of the rudder system. Data showed that during the landing and subsequent rollout, the rudder surface position remained near its neutral position even though the force inputs to the rudder pedals were observed to be increasing. About 30 seconds after touchdown, a significant pedal force input was observed along with corresponding rudder surface movement. Afterward, the rudder pedals and rudder surface began moving as commanded and continued to function normally for the remainder of the taxi.
On February 9, 2024, UAL conducted a test flight on the event airplane at EWR and was able to duplicate the reported rudder system malfunction identified during the incident. As a result, the test flight profile was discontinued, and the airplane returned to EWR and landed uneventfully. The NTSB was notified of the flight control issue after the flight test and an incident investigation was started. Qualified parties were invited to participate in the investigation. These included the Federal Aviation Administration (FAA), United Airlines, The Boeing Company and Collins Aerospace.
NTSB group chairs in the areas of systems and flight data recorders were assigned.The data from the FDR was sent to the NTSB’s Vehicle Recorder Laboratory in Washington, DC, for analysis.
Post-incident troubleshooting and inspection of the rudder control system found no obvious malfunctions with the system or any of its components whose failure would have resulted in the restricted movement observed during flight 1539 and the test flight. As a precaution, the aft rudder input torque tube and associated upper and lower bearings and the rudder rollout guidance servo were removed for further examination by the NTSB systems group.
Following the removal of the rudder system components, UAL conducted a second test flight on the airplane and found the rudder control system operated normally.
Pilot control of the 737-8 rudder is transmitted in a closed-loop system from the pilots’ rudder pedals in the cockpit through a single cable system, aft rudder quadrant, pedal force transducer to the aft rudder input torque tube in the vertical fin. Rotation of the torque tube provides the command inputs to the two main and standby rudder power control units (PCU’s) to move the rudder surface. UAL received the incident airplane from Boeing on February 20, 2023, configured with a rudder SVO-730 rollout guidance servo that was disabled per UAL’s delivery requirements to reconfigure the autoflight system from CAT IIIB to CAT IIIA capability. Although the servo was disabled, it remained mechanically connected to the upper portion of the aft rudder input torque tube by the servo’s output crank arm and pushrod (see figures 1 and 2).
Figure 1. Diagram of rudder control system. (Source: Boeing. Image Copyright © Boeing. Reproduced with permission.)
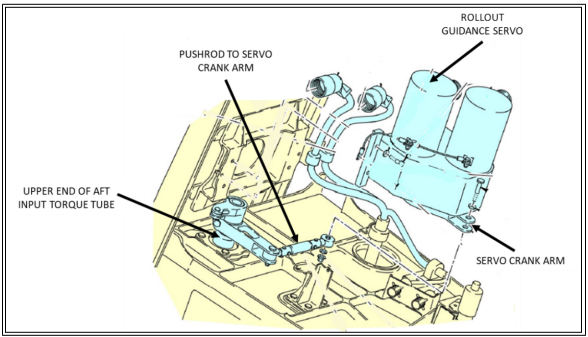
Figure 2. Diagram showing the location of the rollout guidance servo. (Source: Boeing. Image
Copyright © Boeing. Reproduced with permission.)
On February 28, 2024, the Systems group met at the Collins Aerospace facility in Cedar Rapids, Iowa to examine and test the SVO-730 rollout guidance servo removed from the incident airplane. The testing was conducted to evaluate the effects that temperature “cold soaking” of the servo might have on the torque required to move the servo’s output crank arm. Testing at room temperature found that the torque to rotate the servo’s output crank arm was within design specifications. The unit was then “cold soaked” for 1 hour and the test was repeated. That testing found that the torque to move the servo’s output crank arm was significantly beyond the specified design limits. Because the servo output crank arm is mechanically connected to the rudder input torque tube, the restricted movement of the servo’s output crank arm would prevent the rudder pedals from moving as observed during flight 1539 and the test flight. Further examination of the SVO-730 rollout guidance servo will be conducted as the investigation continues.
Read the Preliminary Report
Read Chair Jennifer Homendy's September 30, 2024 letter to the FAA
We provided information to urge The Boeing Company and the Federal Aviation Administration (FAA) to take immediate action concerning the potential for a jammed or restricted rudder control system on certain Boeing 737 airplanes. We identified these issues during our ongoing investigation of the rudder pedal anomaly involving a Boeing 737-8, N47280, while landing at Newark Liberty International Airport (EWR), Newark, New Jersey, on February 6, 2024.
To The Boeing Company:
- Instruct operators of Boeing 737NG and 737MAX airplanes with Collins Aerospace SVO-730 rudder rollout guidance actuators with incorrectly assembled bearings to notify flight crews that the rudder control system might become jammed or restricted in flight or during landing due to moisture that could accumulate and freeze in the actuators. (A-24-27) (Urgent)
- For 737NG and 737MAX airplanes with Collins Aerospace SVO-730 rudder rollout guidance actuators with incorrectly assembled bearings, determine appropriate flight crew responses, besides applying maximum rudder pedal force, if the condition described in Safety Recommendation A-24-27 were encountered in flight or during landing and then notify operators to disseminate this information to flight crews of these airplanes. (A-24-28) (Urgent)
To the Federal Aviation Administration:
- Determine whether Collins Aerospace SVO-730 rudder rollout guidance actuators with incorrectly assembled bearings should be removed from Boeing 737NG and 737MAX airplanes and, if so, direct US operators to remove the actuators until acceptable replacement actuators become available for installation. (A-24-29) (Urgent)
- If you determine the Collins Aerospace SVO-730 rudder rollout guidance actuators with incorrectly assembled bearings should be removed, notify international regulators that oversee operators of Boeing 737 airplanes about the safety issues involving the SVO-730 rudder rollout guidance actuator and encourage them to require the removal of actuators with incorrectly assembled bearings from 737NG and 737MAX airplanes until an acceptable replacement actuator becomes available for installation. (A-24-30) (Urgent)